Facility location problem: Difference between revisions
Lawrenceli (talk | contribs) |
Lawrenceli (talk | contribs) |
||
Line 61: | Line 61: | ||
To determine where the company should build the factory, we will carry out the following optimization problem for each location to maximize the profit from each ton sold: | To determine where the company should build the factory, we will carry out the following optimization problem for each location to maximize the profit from each ton sold: | ||
max <math>\sum_{j\ | max <math>\sum_{j\in J}x_{ij}(100-C_{ij}) </math> | ||
subject to | subject to | ||
<math>\sum_{j\ | <math>\sum_{j\in J}x_{ij} \leq A_i </math> <math>\forall i\in I</math> | ||
<math>\sum_{i\ | <math>\sum_{i\in I}x_{ij} \leq D_j</math> <math>\forall j\in J</math> | ||
<math>x_{ij} \geq 0 </math> <math>\forall i \in I</math> <math>\forall j \in J</math> | <math>x_{ij} \geq 0 </math> <math>\forall i \in I,</math> <math>\forall j \in J</math> | ||
Revision as of 23:43, 21 November 2020
Authors: Liz Cantlebary, Lawrence Li (CHEME 6800 Fall 2020)
Stewards: Allen Yang, Fengqi You
Introduction
The Facility Location Problem (FLP) is a classic optimization problem that determines the best location for a factory or warehouse to be placed based on geographical demands, facility costs, and transportation distances. These problems generally aim to maximize the supplier's profit based on the given customer demand and location. FLP can be further broken down into capacitated and uncapacitated problems, depending on whether the facilities in question have a maximum capacity or not.
Theory and Formulation
Weber Problem and Single Facility FLPs
The Weber Problem is a simple FLP that consists of locating the geometric median between three points with different weights. The geometric median is a point between three given points in space such that the sum of the distances between the median and the other three points is minimized. It is based on the premise of minimizing transportation costs from one point to various destinations, where each destination has a different associated cost per unit distance.
Given points on a plane with associated weights , the 2-dimensional Weber problem to find the geometric median is formulated as(1)
where
The above formulation serves as a foundation for many basic single facility FLPs. For example, the minisum problem aims to locate a facility at the point that minimizes the sum of the weighted distances to the given set of existing facilities, while the minimax problem consists of placing the facility at the point that minimizes the maximum weighted distance to the existing facilities(8). Additionally, in contrast to the minimax problem, the maximin facility problem maximizes the minimum weighted distance to the given facilities.
Capacitated and Uncapacitated FLPs
FLPs can often be formulated as mixed-integer programs (MIPs), with a fixed set of facility and customer locations. Binary variables are used in these problems to represent whether a certain facility is open or closed and whether that facility can supply a certain customer. Capacitated and uncapacitated FLPs can be solved this way by defining them as integer programs.
A capacitated facility problem applies constraints to the production and transportation capacity of each facility. As a result, customers may not be supplied by the most immediate facility, since this facility may not be able to satisfy the given customer demand.
In a problem with facilities and customers, the capacitated formulation defines a binary variable and a variable for each facility and each customer . If facility is open, ; otherwise . Open facilities have an associated fixed cost and a maximum capacity . is the fraction of the total demand of customer that facility has satisfied and the transportation cost between facility and customer is represented as . The capacitated FLP is therefore defined as(7)
In an uncapacitated facility problem, the amount of product each facility can produce and transport is assumed to be unlimited, and the optimal solution results in customers being supplied by the lowest-cost, and usually the nearest, facility. Using the above formulation, the unlimited capacity means can be assumed to be a sufficiently large constant, while is now a binary variable, because the demand of each customer can be fully met with the nearest facility(7). If facility supplies customer , then ; otherwise .
Numerical Example
Suppose a paper products manufacturer has enough capital to build and manage an additional manufacturing plant in the United States in order to meet increased demand in three cities: New York City, NY, Los Angeles, CA, and Topeka, KS. The company already has distribution facilities in Denver, CO, Seattle, WA, and St. Louis, MO, and due to limited capital, cannot build an additional distribution facility. So, they must choose to build their new plant in one of these three locations. Due to geographic constraints, plants in Denver, Seattle, and St. Louis would have a maximum operating capacity of 400tons/day, 700 tons/day, and 600 tons/day, respectively. The cost of transporting the products from the plant to the city is directly proportional, and an outline of the supply, demand, and cost of transportation is shown in the figure below. Regardless of where the plant is built, the selling price of the product is $100/ton.
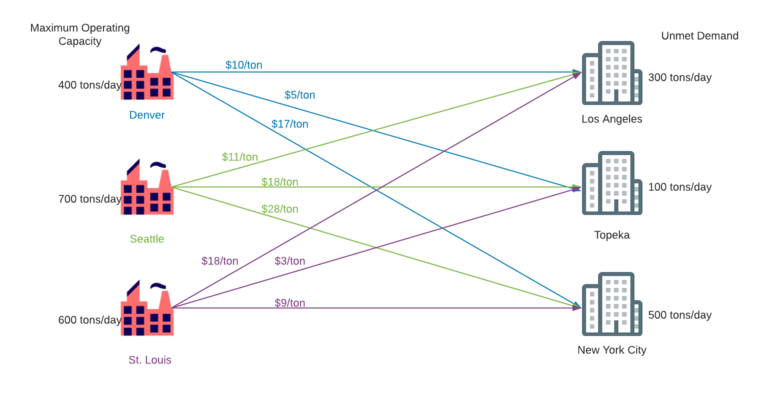
To solve this problem, we will assign the following variables:
is the factory location
is the city destination
is the cost of transporting one ton of product from the factory to the city
is the amount of product transported from the factory to the city in tons
is the maximum operating capacity at the factory
is the amount of unmet demand in the city
To determine where the company should build the factory, we will carry out the following optimization problem for each location to maximize the profit from each ton sold:
max
subject to
If the factory is built in Denver, 300tons/day of product go to Los Angeles and 100tons/day go to Topeka, for a total profit of $36,300/day.
If the factory is built in Seattle, 300tons/day of product go to Los Angela, 100tons/day of product go to Topeka, and 300tons/day go to New York City, for a total profit of $56,500/day.
If the factory is built in St. Louis, 100tons/day of product go to Topeka and 500tons/day go to New York City, for a total profit of $55,200.
Therefore, to maximize profit, the factory should be built in Seattle.
Applications
Facility location problems are utilized in many industries to find the optimal placement of various facilities, including warehouses, power plants, public transportation terminals, polling locations, and cell towers, to maximize efficiency, impact, and profit. In more unique applications, extensive research has been done in applying FLPs to humanitarian efforts, such as identifying disaster management sites to maximize accessibility to healthcare and treatment(4). A case study by Nigerian researchers discussed the application of mixed-integer FLPs in optimizing the locations of waste collection centers to provide sanitation services in crucial communities. More effective waste collection systems could combat unsanitary practices and environmental pollution, which are major concerns in many developing nations(2).
FLPs have also been used in clustering analysis, which involves partitioning a given set of elements (e.g. data points) into different groups based on the similarity of the elements. The elements can be placed into groups by identifying the locations of center points that effectively partition the set into clusters, based on the distances from the center points to each element(9).
Conclusion
The facility location problems is an important application of computational optimization. The uses of this optimization technique are far-reaching, and can be used to determine anything from where a family should live based on the location of their workplaces and school to where a Fortune 500 company should put a new manufacturing plant or distribution facility to maximize their return on investment.
References
- http://www.pitt.edu/~lol11/ie1079/notes/ie2079-weber-slides.pdf
- Adeleke, O. J.; Olukanni, D. O. (2020), Facility Location Problems: Models, Techniques, and Applications in Waste Management. Recycling, 5, 10.
- Balcik, B.; Beamon, B. M. (2008), Facility Location in Humanitarian Relief. International Journal of Logistics Research and Applications, 11, 101-121.
- Daskin, M. S.; Dean, L. K. (2004), Location of Health Care Facilities. Handbook of OR/MS in Health Care: A Handbook of Methods and Applications, 43-76.
- Drezner, Z; Hamacher. H. W. (2004), Facility Location Applications and Theory. New York, NY: Springer.
- Eiselt, H. A.; Marianov, V. (2019), Contributions to Location Analysis. Cham, Switzerland: Springer.
- Francis, R. L.; Mirchandani, P. B. (1990), Discrete Location Theory. New York, NY: Wiley.
- Hansen, P., et al. (1985), The Minisum and Minimax Location Problems Revisited. Operations Research, 33, 6, 1251–1265.
- Meira, L. A. A.; Miyazawa, F. K.; Pedrosa, L. L. C. (2017), Clustering through Continuous Facility Location Problems. Theoretical Computer Science, 657, 137-145.